The 10 Best Ways to Value Engineer a Construction Project
- stuart8035
- Oct 17, 2023
- 2 min read
In the realm of construction, efficiency, cost-effectiveness, and innovation play pivotal roles in ensuring the success of a project. Value engineering is a systematic method that aims to improve the value of goods or products and services by using an examination of function. When it comes to construction projects, value engineering is a critical process that can significantly impact the project's outcome. To ensure the success and efficiency of a construction project, here are the ten best ways to value engineer:
1. Functional Analysis and Evaluation: Undertake a thorough analysis of the project's functional requirements. Identify the core purpose and intended use of the structure to ensure that every design element serves a practical function.
2. Cost-Benefit Analysis: Conduct a comprehensive cost-benefit analysis for every design decision. Prioritise elements that provide the most significant functional benefits at the most reasonable cost.
3. Material Selection Optimisation: Explore alternative materials that meet the required standards and regulations. Consider durable, sustainable, and cost-effective materials that align with the project's requirements without compromising quality.
4. Streamlining Design Processes: Foster collaboration among architects, engineers, and contractors to streamline the design process. Implementing integrated design strategies can help identify potential issues early and promote a more efficient workflow.
5. Innovative Technology Integration: Embrace innovative technologies and construction methods to streamline operations, enhance productivity, and reduce costs. Integrate digital tools such as Building Information Modelling (BIM) and other advanced software solutions to improve project planning and management.
6. Optimised Construction Techniques: Explore innovative construction techniques that can expedite the construction process without compromising quality. Prefabrication, modular construction, and other modern methodologies can significantly reduce labour costs and project timelines.
7. Energy Efficiency Solutions: Incorporate energy-efficient systems and sustainable practices into the project design. Implementing renewable energy sources, efficient insulation, and smart building technologies can reduce operational costs and enhance the project's long-term sustainability.
8. Risk Management and Mitigation: Identify potential risks and challenges early in the project lifecycle. Develop comprehensive risk management strategies to mitigate potential delays, cost overruns, and other unforeseen obstacles that could impact the project's overall value.
9. Life-Cycle Cost Analysis: Consider the long-term costs associated with maintenance, repairs, and operational expenses. Opt for designs and materials that offer longevity and require minimal upkeep, thereby reducing life-cycle costs and ensuring long-term value.
10. Continuous Communication and Feedback Loop: Maintain open communication among all stakeholders throughout the project. Encourage feedback and constructive criticism to foster a collaborative environment that promotes continuous improvement and value optimisation.
Implementing these ten best practices for value engineering in construction projects can lead to enhanced efficiency, reduced costs, and improved overall project value. By prioritising functionality, cost-effectiveness, and innovation, construction professionals can ensure the successful execution of projects while maintaining the highest standards of quality and sustainability. If you are not value engineering every project, you should be. If you need help with putting these VE systems into place then please contact us here at TTP as we tried & tested methods to be able to do this.
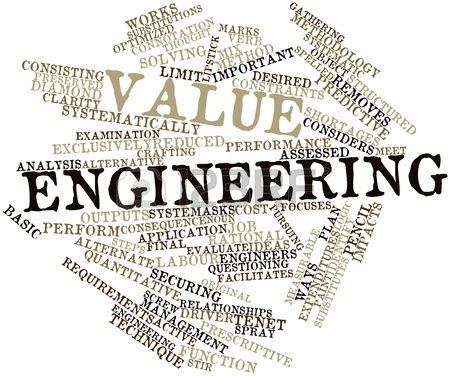
Comments